A CAUTIONARY CASE STUDY: MINNEAPOLIS, MINNESOTA, USA
Investor-owned & municipal utilities may experience catastrophic damage if it relies on Untethered Acoustic Ball technology to locate leaks. As shown below, the inspection of a 10,000-feet (3km) of 36-inch (913mm) diameter Prestressed Concrete Cylinder Pipe (PCCP), gave a clean-bill-of-health with ‘NO LEAKS’ using a leading vendor’s Untethered Acoustic Ball technology. Eighteen (18) months later, separate pipe ruptures occurred. First, on June 21, 2013 (Rupture #1) causing a 30ft-wide by 15ft-deep hole, followed by a second rupture on September 19, 2014 (Rupture #2), located nearby the first ruptured pipe. Not disclosed to local media, both pipe failures had ‘NO LEAKS’ identified using sensitive listening devices equipped with acoustic sensors sent through the pipe a caught in netting downstream from its insertion point.
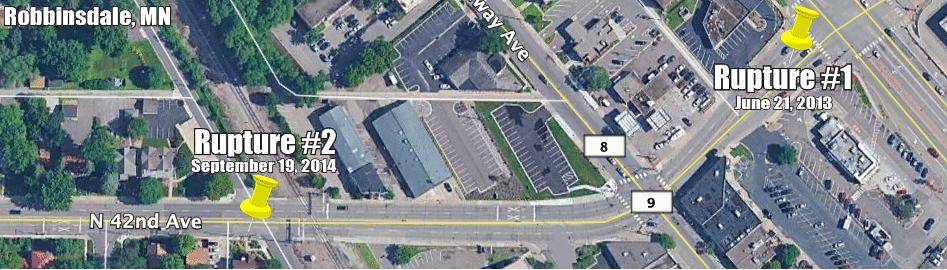
Both ruptures cost over $2 million, each, to repair, excluding damages to local businesses that were flooded due to the rupture of both pipes. As shown in Figure 2 (Below), the five-lane roadway underwent severe damage, located in a high traffic area in front of a McDonalds restaurant.
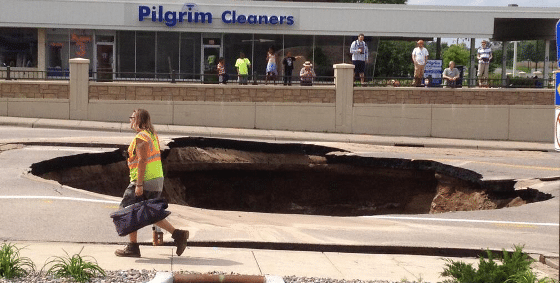
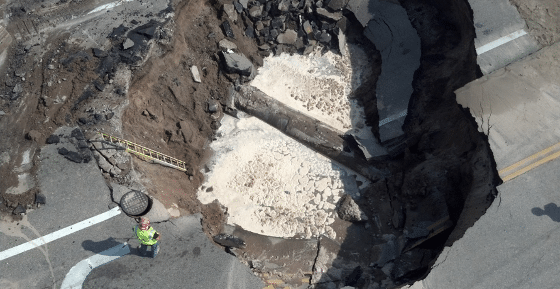
Causing $2.4 Million in Construction Repairs.
Figure 3 shows the exhumed pipe from Rupture #1, where pre-existing cracks and pipe deterioration indicated constant and ongoing leakage that was not detected up by the Untethered Acoustic Ball contractor, that also supplied its own technology licensed from a UK water organization. The supplier knew that leakage in pipes pressurised below 70 psi would be difficult to hear using its untethered acoustic foam-encased hydrophone ball. The operator of the pipeline already knew that a number of false-positive readings would occur from the ball bouncing along the side of the pipe, but, feared damage from major changes in pressures to facilitate acoustic inspection.
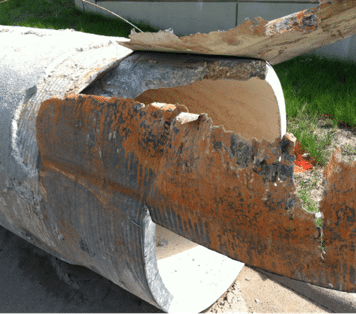
Fifteen (15) months later, a second rupture occurred less than 3,000 feet (1km) away from the first location. As shown in Figure 4, the second segment of the 36-inch (914mm) diameter pipe also ruptured under the same five-lane arterial collector roadway in the same business area – in front of an office and apartment building – where no leaks were found using an Untethered Acoustic Ball.
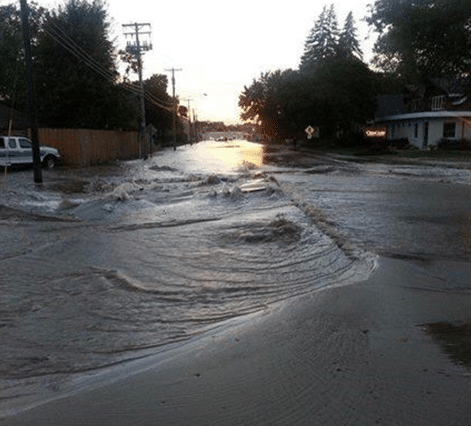
Again, the exhumed pipe responsible for Rupture #2 showed clear and unambiguous evidence of cracks and leakage, Figure 5, not detected by untethered acoustic ball technology.
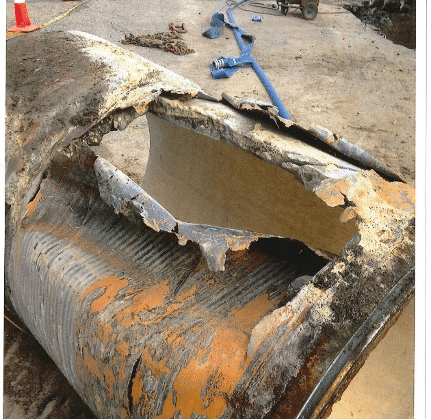
The second rupture measured 1,300 ft (0.4m) and dewatered for repairs. Upon further investigation to determine the cause, the owner responsible for the pipeline entered into a second contract with the same Untethered Acoustic Ball supplier to insert an electro-magnetic scanner, as shown in Figure 6, at an additional cost of $137 per meter, to assess the damaged pipe.
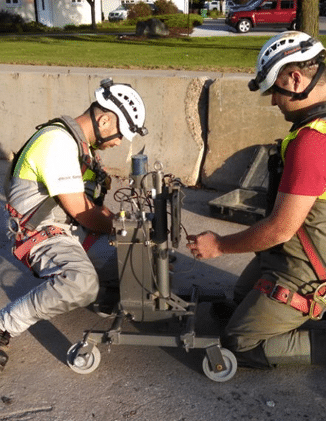
to Enter the Pipe After Rupture #2.
During that electro-magnetic scan, supported by human-entry, cracks and other defects were found in the pipe wall and photographed, shown in Figure 7.
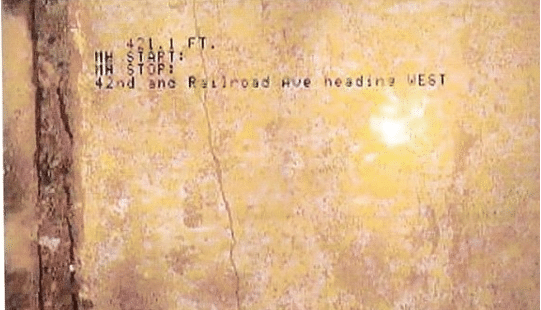
Missed by Untethered Acoustic Ball, Found During Human-Entry.
The usual failure mode of PCCP walls rarely are catastrophic. Instead, research indicates that give PCCP provides advance warning of failure by leaking. Small and slow at first, then quicker as openings widen. A wall can leak for a long time before it ruptures catastrophically as shown in Figures 2 and 4. However, spheres cannot hear small leaks without first dramatically increasing the pressure inside the pipe to make the leak noisier. Even if Electro Scan’s Delta probe cannot hear the leak using its acoustic sensor; it would have detected, located, and estimated in LPS the size of small leaks through small cracks using electrical current.
Details of this study may be requested by contacting Electro Scan Inc.
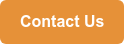